Case study on machine vision enabled quality control for Solar Panel manufacturer
How Apex Vision reduced test time by 83%
The client, an established solar panel manufacturing company, was facing inefficiencies in accurately identifying defective cells and interconnects, leading to potential performance issues and reduced panel efficiency. Additionally, the manual quality control (QC) testing procedures were time-consuming, resulting in increased production costs and delayed time-to-market. Furthermore, the absence of detailed data hindered the client’s ability to conduct thorough root cause analysis, limiting their capacity to address underlying issues and optimize manufacturing processes effectively.
Thus, the primary challenges revolved around the identification of bad cells and faulty interconnects, coupled with the need to streamline manual QC testing processes and generate comprehensive data for root cause analysis.
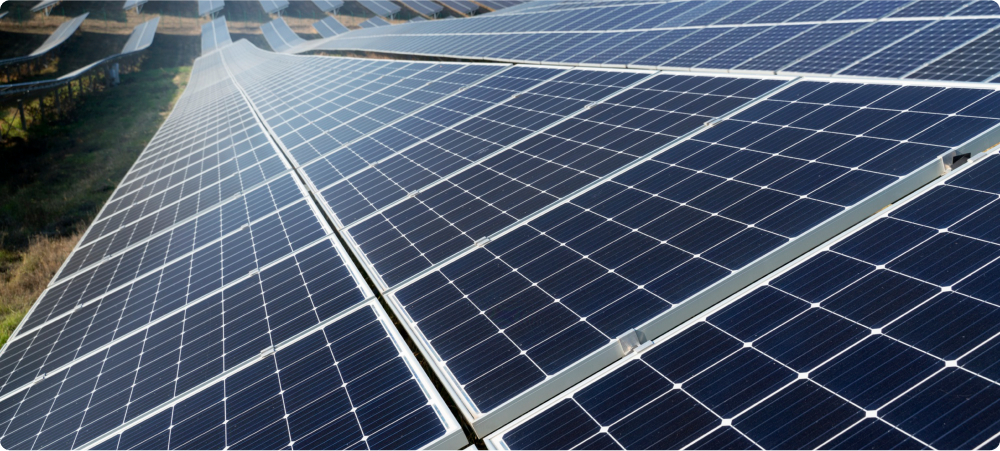
Business Needs
- Identification of bad cells and faulty interconnects.
- Streamline manual quality control (QC) testing processes.
- Generate comprehensive data for root cause analysis.
Solution
- Established a full-fledged Al-based inspection system.
- • Integrated the newly developed Al system with the Manufacturing Execution System (MES), enabling the identification of testing conditions from previous inspection steps and ensuring consistency in quality control protocols.
- Engineered utility tools tailored for image analysis, featuring overlays and visualization enhancements, to facilitate in-depth defect analysis for yield improvement projects.
- Facilitated the generation of detailed data sets, providing valuable insights for root cause analysis, thus optimizing manufacturing processes, and enhancing overall product quality and efficiency.
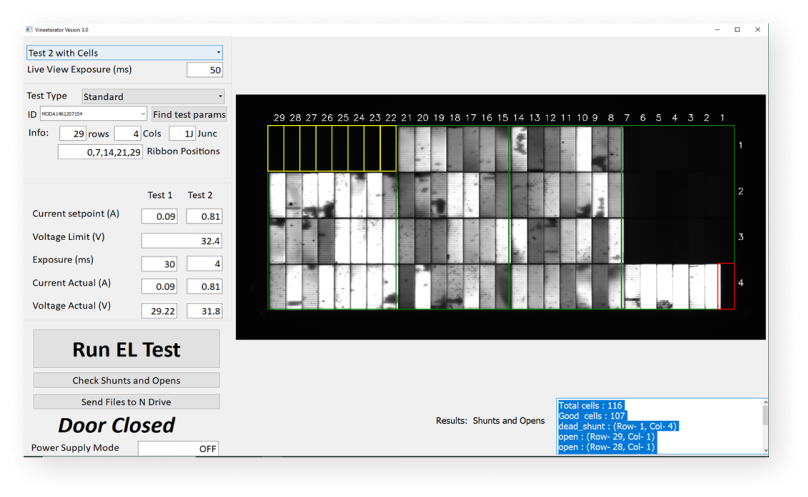
Imapct
- Substantial improvement in test time efficiency, reducing test time from an onerous 30 minutes to a mere 5 minutes.
- Eliminated the need for photoluminescence testing, a time-consuming and resource intensive step in the quality control process. This resulted in savings costs and increasing operational efficiency.
- Significantly reduced the need for human interpretation in the inspection process by leveraging advanced visual Al algorithms and image processing techniques. This lead to automated defect detection, minimizing errors and variability associated with manual interpretation.